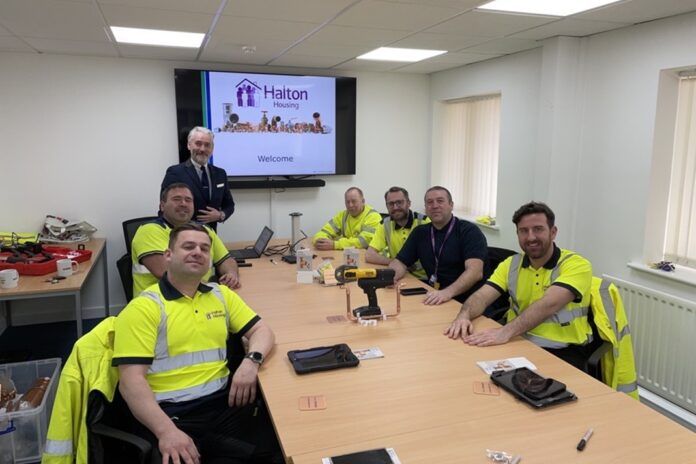
Halton Housing reported that it is making significant savings in time and money using press-fit technology.
The housing association converted to press-fit after consulting Conex Bänninger.
Steve Bounds, Halton Housing’s lead gas technician, said: “Our initial interest in press-ft began following a health and safety initiative which convinced us that the only way to eliminate the risk of fire was to look at alternatives to on-site brazing. This move was welcomed by our team who are active on social media and could see how many installers had converted to press and rated it very highly.
“My colleague, gas manager Kevin O’Neill and I met with Noel Kelly from Conex Bänninger and decided to initially trial the company’s 15mm and 22mm >B< Press products for gas applications and everything has grown from there. Our relationship with Noel is first-class and his knowledge and willingness to help is much appreciated. He has visited us on numerous occasions and we always welcome his advice.”
According to a statement, >B< Press fittings are 3-point press which adds a further layer of security when joining pipes and are compatible with a range of press tools and jaws. They are flame-free and are suitable for a range of applications including drinking water, heating systems, hot and cold water, gas, solar and renewables.
Steve added: “Knowing that you have a good seal with every joint gives you ‘peace-of-mind’ that once it’s done you won’t need to go back and undertake a repair. Once the initial preparation has been done, the joint takes just five seconds to create, which is so much faster than brazing.
“The initial cost of a press machine can be quickly recouped because the speed of installation reduces the amount of time needed on site, and there are significant savings to be made in the purchase of consumables, such as flux, heat resistant mat, solder, soldering torch and gas canisters. We initially bought a single Rothenberger press tool and the return on investment (ROI) on this was recouped fairly quickly, with a second gun purchased later.
“It’s mainly the installation lads that use the press machines and they’re all fighting for them whenever they get a job! We use >B< Press primarily on boiler swaps for the couplings, the elbows and one of our team has asked if we can start using them on 45-degree bends.
“Our engineers have been brought up on brazing and there are still occasions when it is used, but it’s press 95% of the time. The number of jaws that are now available for use in conjunction with the press machines including mini jaws and adjustable jaws, which means that there aren’t many situations where you can’t use the press machine with the fittings.
“The Conex Bänninger brand is one that you can trust with a heritage stretching back 115 years with its products being manufactured to a high quality and backed-up by a first-class service.”
Noel Kelly added: “I have a great working relationship with Steve and Kevin, who are both open to change and doing things differently. I have undertaken a couple >B< Press training sessions, which were well received by their team. I will continue to support them with advice and visit ‘on-site’ whenever needed.”